Enabling robotic assembly of the final product is one of the key advantages of Q5D’s approach. With our machines integrating wiring into the component parts and assemblies, the final product can be assembled by machine as well.
Q5D has been working with an manufacturer to create components that become functional when plugged into their vehicles. One area of development is the battery management system of an electric vehicle (EV).
All EVs use battery management systems to join together the individual cells that make up the battery system. Assembling the cells into a rigid case allows for easier installation into the vehicle. Q5D has studied how this case can be wired using our machine allowing the battery cells to become functional once they are installed in the case by a conventional industrial robot. The whole case can then be installed in the vehicle robotically and become functional.
As part of the study a concept video was produced.
The conclusion of the study was a detailed bill-of-materials and takt time calculations showing that Q5D was able make the battery management system for a total cost equivalent to that from the least expensive imported solution, without any compromise in quality compared to existing sources. For the vehicle manufacturer the cost savings and productivity gains occur because the assembly onto the chassis can be automated.
The remaining challenges are to demonstrate reliability and repeatability of production at scale and further develop the use of automotive terminations.
Benefits
- Automated wiring of battery management systems (BMS)
- Enabling automated final assembly
- Takt time reduction for BMS and final vehicle
- C0-located production

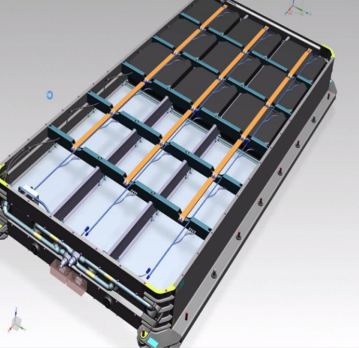
Ready to see this in action?
Contact us to discuss your project.