Electric vehicle makers race to automate wire harnesses
Ready to see Q5D in action?
Contact us to discuss your project.
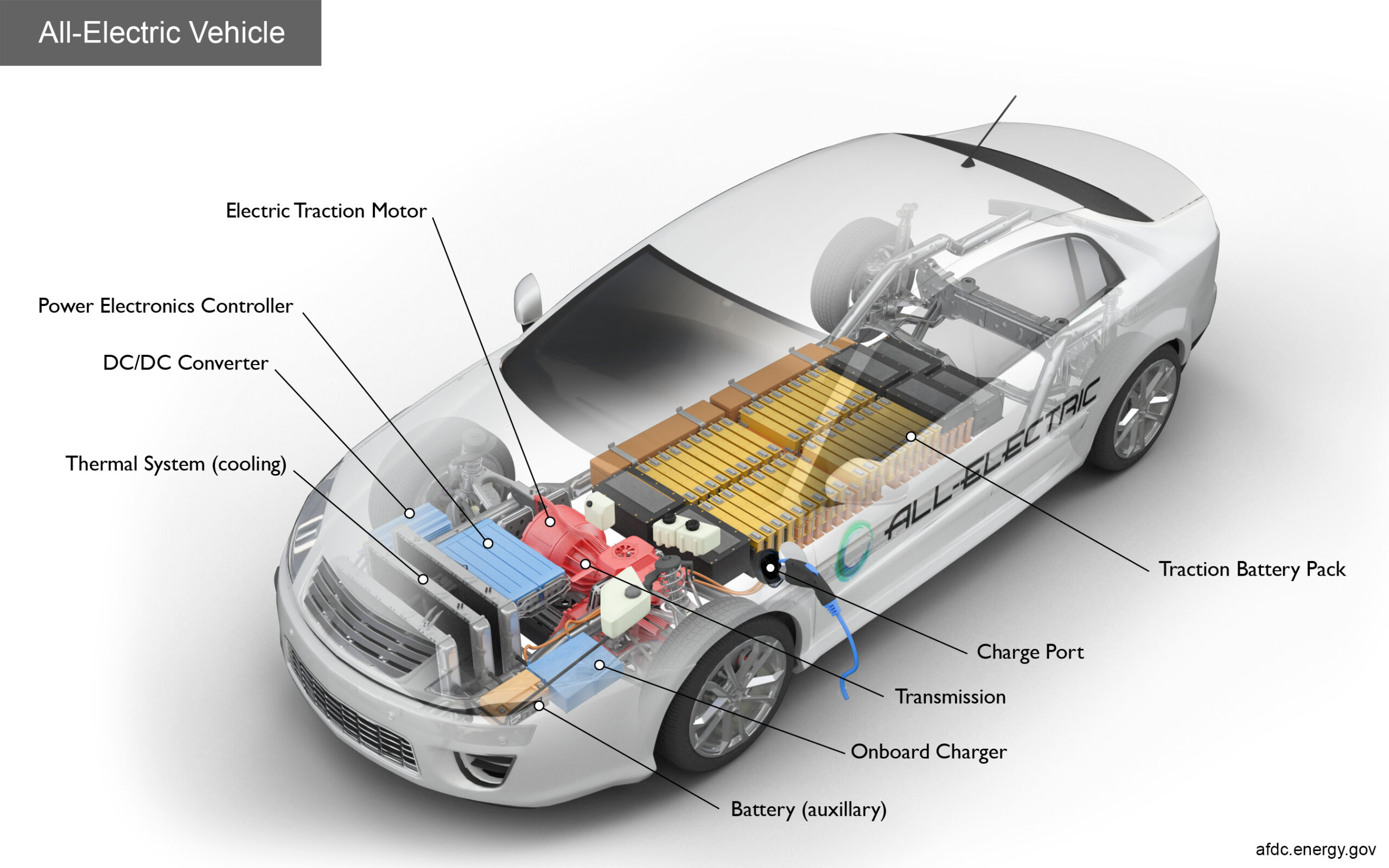
In the electric vehicle (EV) market, global competition is fierce, as demonstrated by recent price falls from leading players. Manufacturers are seeking cost and performance advantages over competitors. A vehicle’s wiring harness, which connects all the electrical and electronic circuits, is one of the largest and heaviest components bought by EV makers. It is also the last major barrier to fully automated manufacturing and all the benefits it could bring. Here’s why the issue is being addressed so urgently and how wire harness automation will make EVs more competitive in every way.
Vehicle wire harnesses are safety-critical components in cars, and particularly so for EVs equipped with ADAS and autonomous driving technologies. Cars are becoming more reliant on electronics and EVs are packed with sensors and actuators that regulate and protect every aspect of drive trains. In addition, wire harnesses feed signals and power for driver convenience functions, such as heated seats, and for infotainment, navigation, and communications systems.
The problems arising from manual wire harness production
- The manual process itself: produced by hand, harnesses are increasingly complex and expensive to manufacture.
- Supply chain complexity and risk: because production is labor-intensive, harnesses are produced in countries with low labor costs. However, final assembly typically takes place thousands of miles away. This adds transportation costs, complexity, and risk to the supply chain. The war in Ukraine, where many wire harnesses are made for European car markets in particular, devasted supply chains and throttled overall vehicle sales.
- The need for 100% test: every circuit must be tested in every manually produced wire harness. This is because the process is so prone to errors. Automated wiring would likely only need sample testing because of the more consistent quality that’s achievable.
- The need to over-order: quality issues are so common that some car maker executives have stated they need to over-order substantially to ensure they have sufficient inventory of acceptable quality. With each harness costing around $1,000 to $2,000 for a typical mid-range EV, this represents significant wastage.
- The need to over-specify: every conventional harness wire must use insulated wires to prevent short circuits, adding insulation weight and cost. Also, wires often need to be heavier than the electrical requirement demands so that they can withstand the physical pressures encountered during assembly and when the vehicle is being driven. Adding unnecessary weight to an EV compromises its range, and shorter range means consumers expect to pay less for vehicles.
- Rework during assembly: quality issues are encountered when harnesses are manually bent and twisted during final assembly.
- Warranty repairs and vehicle recalls: warranty claims are expensive to address and vehicle recalls even more so. In 2022, CNET reported that Nissan had recalled nearly 700,000, 2014-2016 Rogue SUVs over fire risk. The issue was caused by a badly sealed wiring connector. For the same year, the US National Highway Traffic Safety Administration (NHTSA) cited electrical system issues as accounting for 20% of all car recalls.
- Brand reputation: the cost to brand reputation of vehicle recalls is incalculable but can run into many tens of millions of dollars.
With all these issues in mind, research financed by the European Regional Development Fund and published in March 2023, concluded that “automation in the wiring harness industry still constitutes the biggest deficiency. Despite research findings and patents, to our knowledge, none of these solutions have been implemented in the field and the state-of-the-art manufacturing process is still highly labor-intensive.”
How electrical function integration is rising to these challenges
There have been many attempts to address the wire harness challenges described here. Companies have claimed to offer wire harness automation but on closer inspection, the limitations of these processes become apparent. Most automation machines simply bundle wires together and, in some instances, affix connectors to the ends of the wires. There is inevitably a lot of manual work still to be done and most of the problematic issues, including the weight, fragility, and the length of supply chains, remain.
However, a new hybrid additive manufacturing and automation process promises a much higher degree of automation. An ‘electrical function automation’ robot cell enables the full or partial replacement of traditional wire harnesses. It eliminates, or at least mitigates, the need for the manual processes of adding electrical conductors to everything from EV battery packs to cars’ infotainment systems. A precision 5-axis robot with interchangeable tools can add 3D polymeric features to metal, ceramic, or polymer surfaces. It can handle complex shapes, add bare or insulated wires, and attach electrical connectors to make the component functional. The robot can route wires with conductors up to 3mm in diameter, which is around 13 AWG. This means each conductor can carry over 20 amps, sufficient for low-level signals and power functions such as operating relays or fans.
Anchoring each wire to a substrate is fast, cost-effective, and flexible. The substrate can be the component itself, for example a battery pack, or a part designed to carry the wiring for subsequent attachment to the component. It can be rigid or flexible. Because each wire is individually secured, it may not require insulation, saving cost and weight. In addition, it is far less prone to environmental and mechanical damage because it’s securely positioned.
The finished products or components with integrated wiring also lend themselves to robotic final assembly, and the reduction in the labor content means that cost-effective manufacturing can be undertaken in many more places. This can eliminate supply chain risks by co-locating the integration of electrical conductors and components with the vehicles’ final assembly.
The race to compete in wiring automation is intense
In vehicle manufacturing, particularly for EVs, automating the manufacture of much of the wire harness content will not only increase productivity. It will reduce the size and weight of sub-assemblies and their component parts and enable onshoring of manufacturing processes. It will increase vehicle reliability, cut after-sales warranty and recall costs, and protect the value of the brands in which automakers invest so much to build. The 5-axis robotic cells described here are currently being evaluated by a number of global car makers, and will be integrated into EV manufacturing lines within the next 12-18 months. Who will take pole position, we wonder?
Note: An earlier version of this article was previously published in by EV Engineering here and in both German and Italian in leading trade media outlets.