Electrical Wire Processing Technology Expo (EWPTE) 2024 – Review
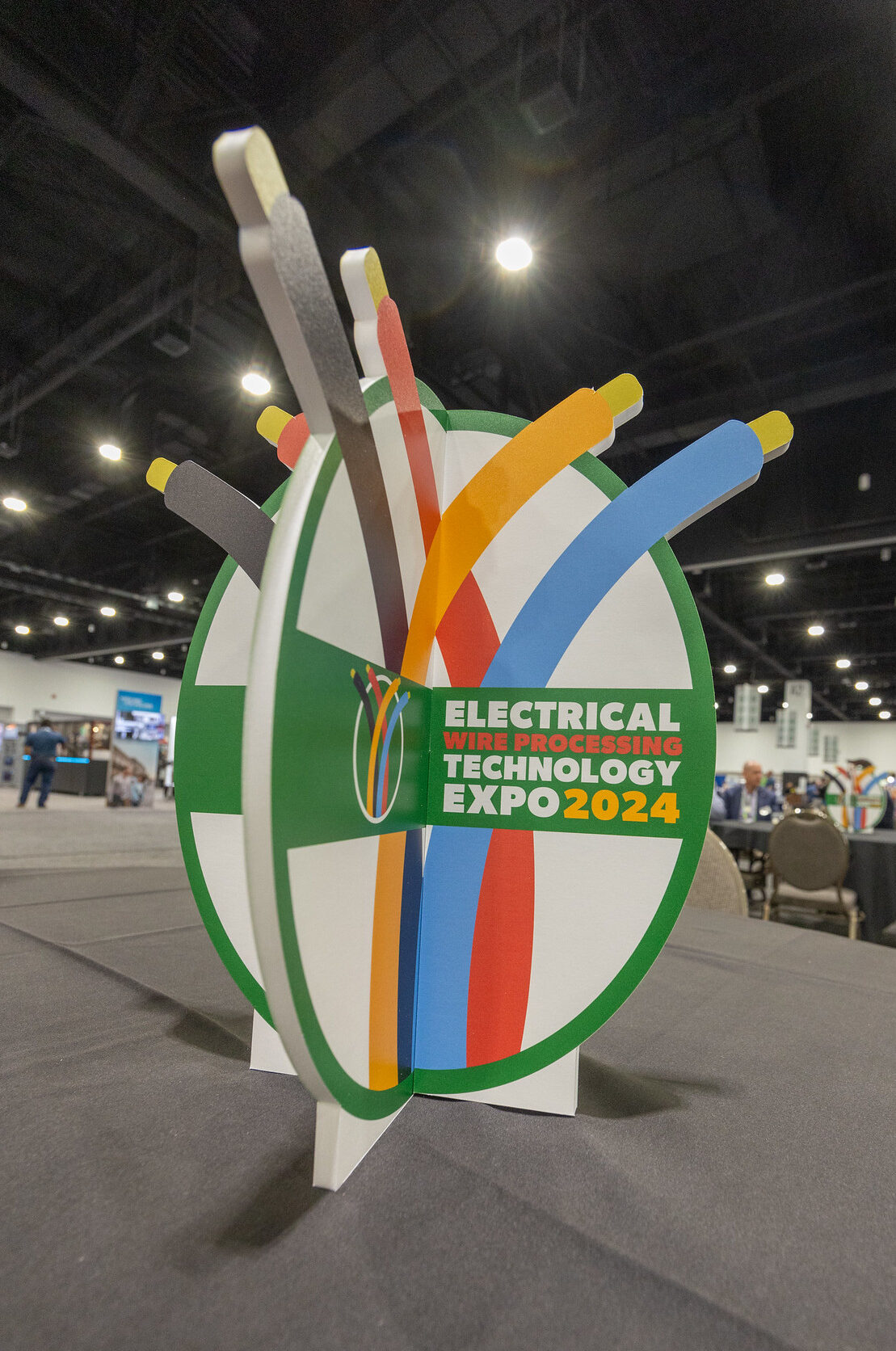
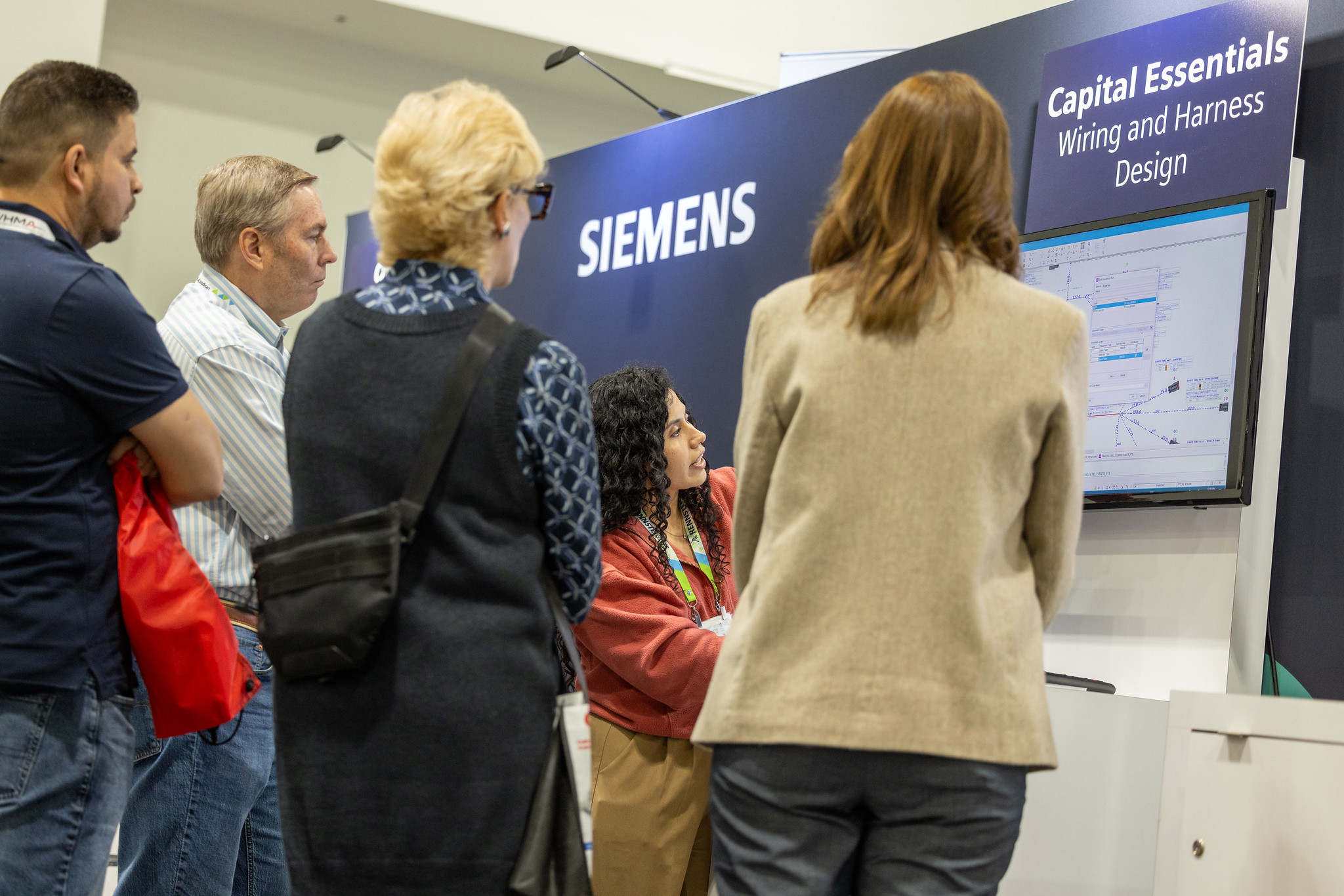
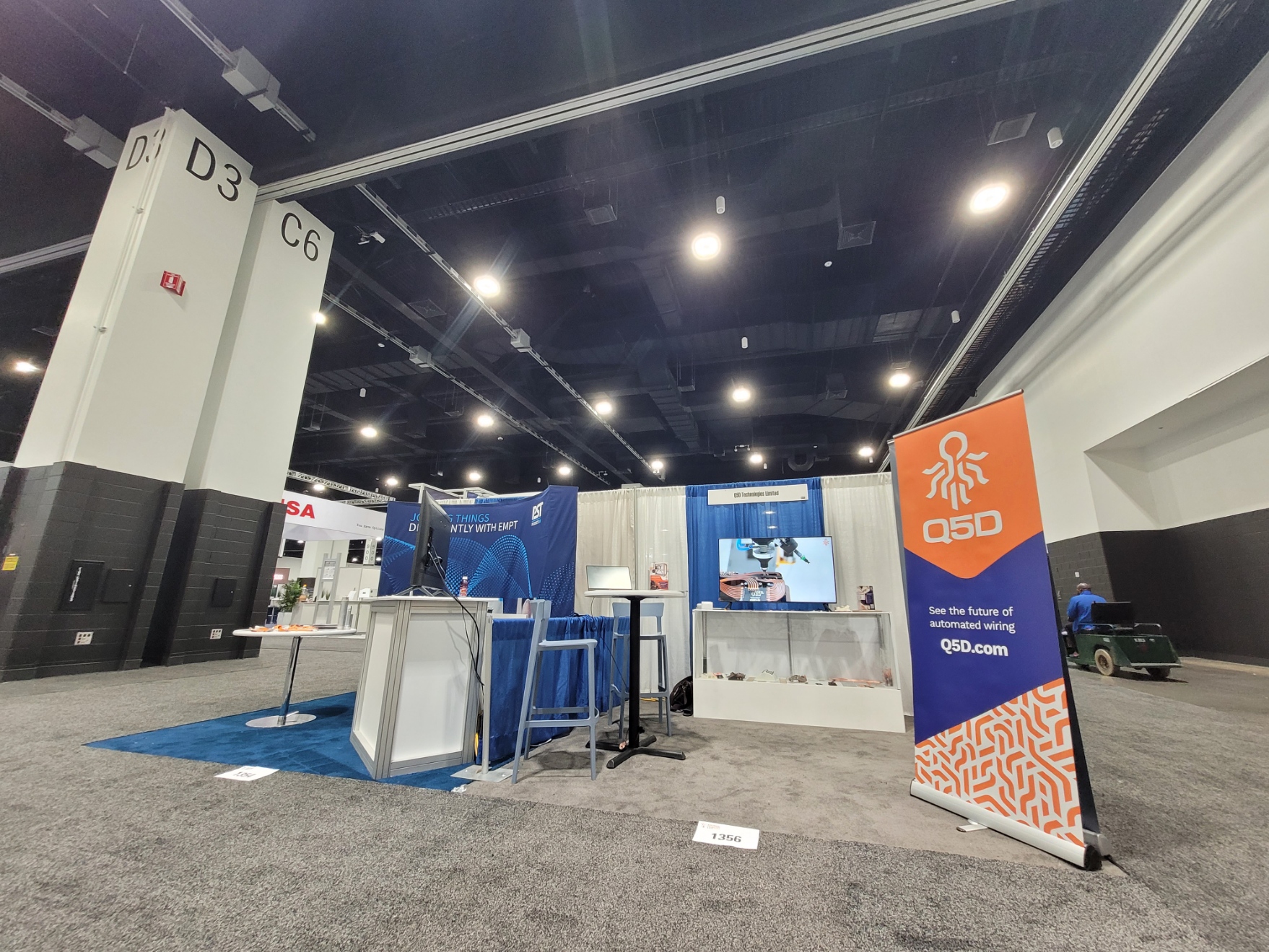
Ready to see Q5D in action?
Contact us to discuss your project.
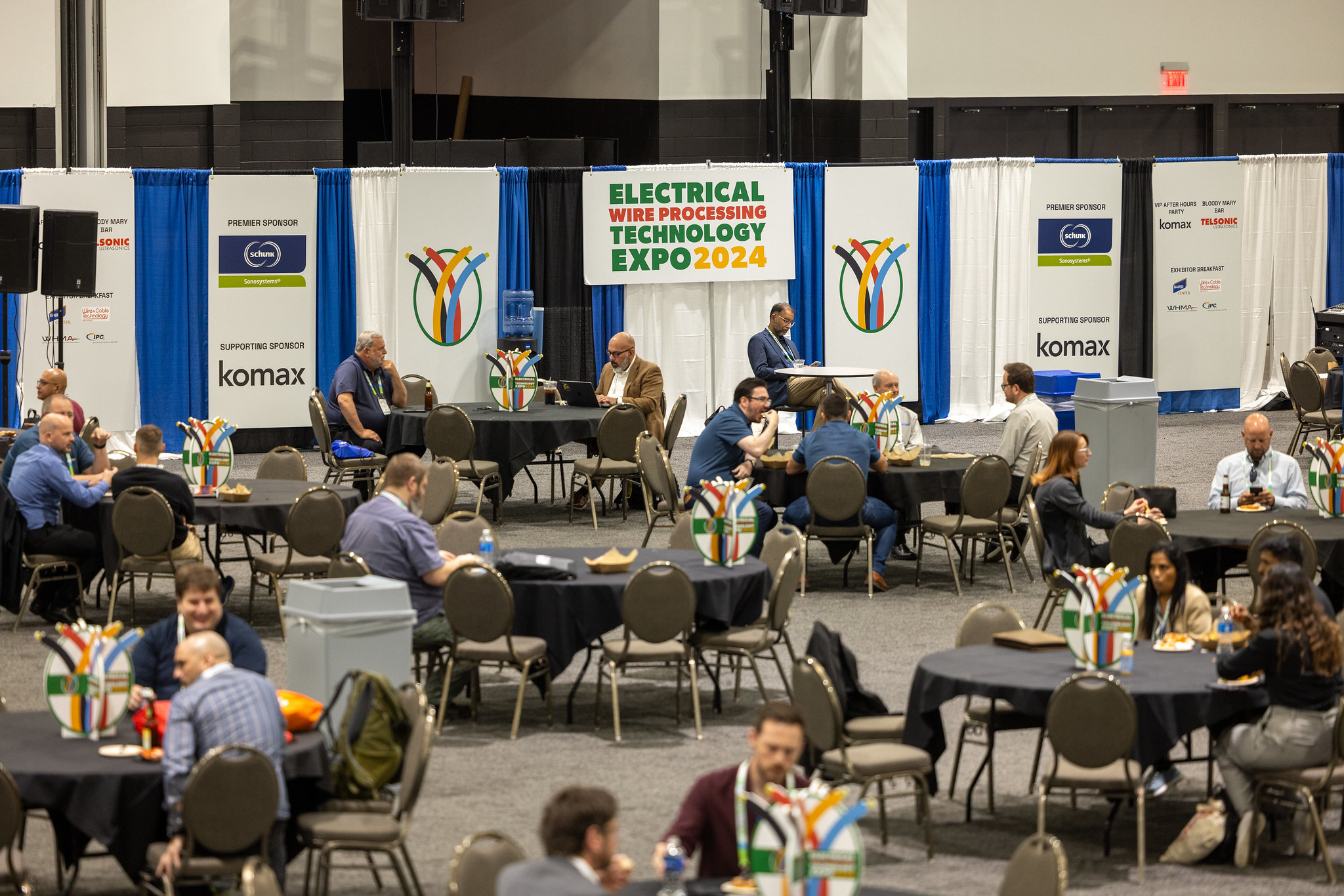
Electrical Wire Processing Technology Expo (EWPTE) is an annual trade show and conference in Milwaukee USA which specialises in wiring harness production and supply. https://www.electricalwireshow.com/
Q5D exhibited at this show for the first time in May 2024. Over the course of the 3 day conference and 2 day trade show we enjoyed the opportunity to share our unique approach to harness production in an event dedicated entirely to wire harnesses. The town of Milwaukee and the facilities were very welcoming and Lake Michigan disappearing over the horizon is spectacular. Do not leave Milwaukee without trying the Caramelized Brussels Sprouts from Swingin’ Door Exchange (great value and service in a perfect atmosphere).
For me it was exciting to see every aspect of harness sourcing and production in one space and to have access to a lot of generously shared knowledge. There were booths offering specific products for wire coating, stripping, crimping, ultrasonic welding, coiling, taping, mounting, harness board assembly and accessories.
Larger booths showed the current level of automation available to a wire harness producer. Machines which feed a wire, strip and crimp each end and offer a stack of these prepared wires for further processing into a harness on another station or facility. Harness board assembly showed projection and display tools to help a manual worker but nothing like the complete Q5D automation method.
Software to design harnesses and output instructions for machinery has digitised a lot of the work to prepare parts of a harness. The influence and control of the design software seems to end at this stage. Our own software toolchain would maintain a digital twin of each component for quality control and traceability.
Interesting too were the number of delegates and exhibitors from Mexico and regions of Asia, it is clear that the cost of labour makes these regions very important to the market. Most of our conversations included labour concerns around rising demand for harnessing with reducing workforces availability.
The generosity of knowledge was exceptional in Professional Development Courses presented by recognised experts in wire processing.
Some highlights include:
Basics of Ultrasonic Metal Welding Instructor/Speaker: Home Mojal, Special Systems Sales Manager, Telsonic
In this session we learned of the technical challenges of creating a good weld with some great advice on how to overcome them.
Magnet Wire Insulation Piercing Connectors: Connector Selection and Validation for Magnet Wire Workshop Instructor/Speaker: Henry Stefanov, Product Marketing Specialist, ABB Inc
I joined this session late due to overlapping schedules but what I saw was a very detailed presentation on variations in insulation for magnet wire and their primary application and an excellent Q&A session.
Electrical and Electronics Protection: Low Pressure Molding Instructors/Speakers: Terry Ng, Lead Materials Scientist & Alek Poniatowski, Lead Mechanical Design Engineer, LPMS-USA
This session focussed on the benefits of low pressure moulding over competing ingress protection methods. I was convinced by the end.
Software Defined Vehicles (SDV) in All Forms of Transportation- Will this Trend Decimate the Wire Harness Industry? Instructor/Speaker: Paul Johnston, Portfolio Development Executive, Siemens Digital Industries Software
My colleague Simon Baggott attended this session and frequently referenced the insights from a very engaging presenter, Paul, who we met at the Siemens Capital booth. Automotive customers face real challenges of cost, space and weight, and reducing complexity of wiring by moving to a “zonal architecture” approach can help with all of these problems. Companies like Ford have made this central to their development plans.
Automation in Harness Construction & Emerging Technologies Instructor/Speaker: Lee Humphreys, Regional Sales Manager, Komax Corporation
Komax was a sponsor of the show this year and certainly made a big impression. They provide machinery which can prepare a lot of the wire harness components which are later assembled into a harness manually. We were excited to see the “Emerging Technologies” and encouraged to see that, even in a presentation from a leader in the field, our approach is still the only way that assembly of a harness has been completely automated.
Digitalization & Future Readiness for Automation Instructor/Speaker: George Tilli, Digital Product Manager, Komax Corporation
George presented a data driven approach to managing the parts of a harness. It seems that the future readiness is still only a list, even in database form. While this improves a paper list or a basic spreadsheet the Q5D system includes a digital twin for every part of every harness we make so a part can be traced back to a batch of materials with logs of each process all the way to when the customer picks up the vehicle, through servicing, right through to the point it enters end of life recycling.
EWPTE is an excellent trade show demonstrating tools and techniques which impact every electrical device made today, I am certain Q5D will create even bigger waves in the 2025 event. The exhibits provided a detailed picture of the status of the industry, the range of machinery available for preparing wires and gave Q5D an opportunity to show our vision for the future. This vision was easy to accept for a stream of harness manufacturing experts – automation is so obviously needed. Every conversation turned to labour shortages or lack of availability in production (linked to labour shortages).
Q5D wont replace everything in the array of machinery and supply of materials exhibited. A large selection of the demonstrated stripping and crimping machines, design software, consumables and materials are still part of our toolchain. Our method is compatible with most existing devices, many of the tools could be integrated and complimentary to our automation system.
Despite repeated claims of automation, the assembly of the harness is clearly still reliant on manual labour. This is the most complex, and expensive, part of a harness and Q5D were the only exhibiting company demonstration automated wiring harness production from digital design to assembly in the final product.