Near Field Communication of all kinds needs an antenna. In this instance the customer was seeking a way of simplifying the supply chain.
The existing part requires a 5-step manufacturing process, with an injection moulding, and a stamped metal part glued together. The conductor is then being cut and spring contacts spot welded onto the tracks.
Q5D was able to demonstrate how a single bare wire could be laid onto the injection moulded part despite the complex surface.
With automated pick, place and termination of the conductor wire, only two manufacturing steps are required. Injection moulded bases are loaded into the manufacturing cell, and all other steps carried out by the machine automatically.
Upto 50 parts can be processed at a time using the CY1000 manufacturing cell. The small footprint and elimination of labour content means that co-location of the production of this component with final assembly of the product can be enabled .
The project is ready to commence the volume prototyping and qualification stage.
Comparison of manufacturing approaches
Attribute |
Current |
Q5D solution |
% improvement |
---|---|---|---|
Manufacturing steps | 5 | 2 | 60 |
Takt time (sec) | 120 | 15 | 87 |
Lead time (days) | 30 | 0 | 100 |
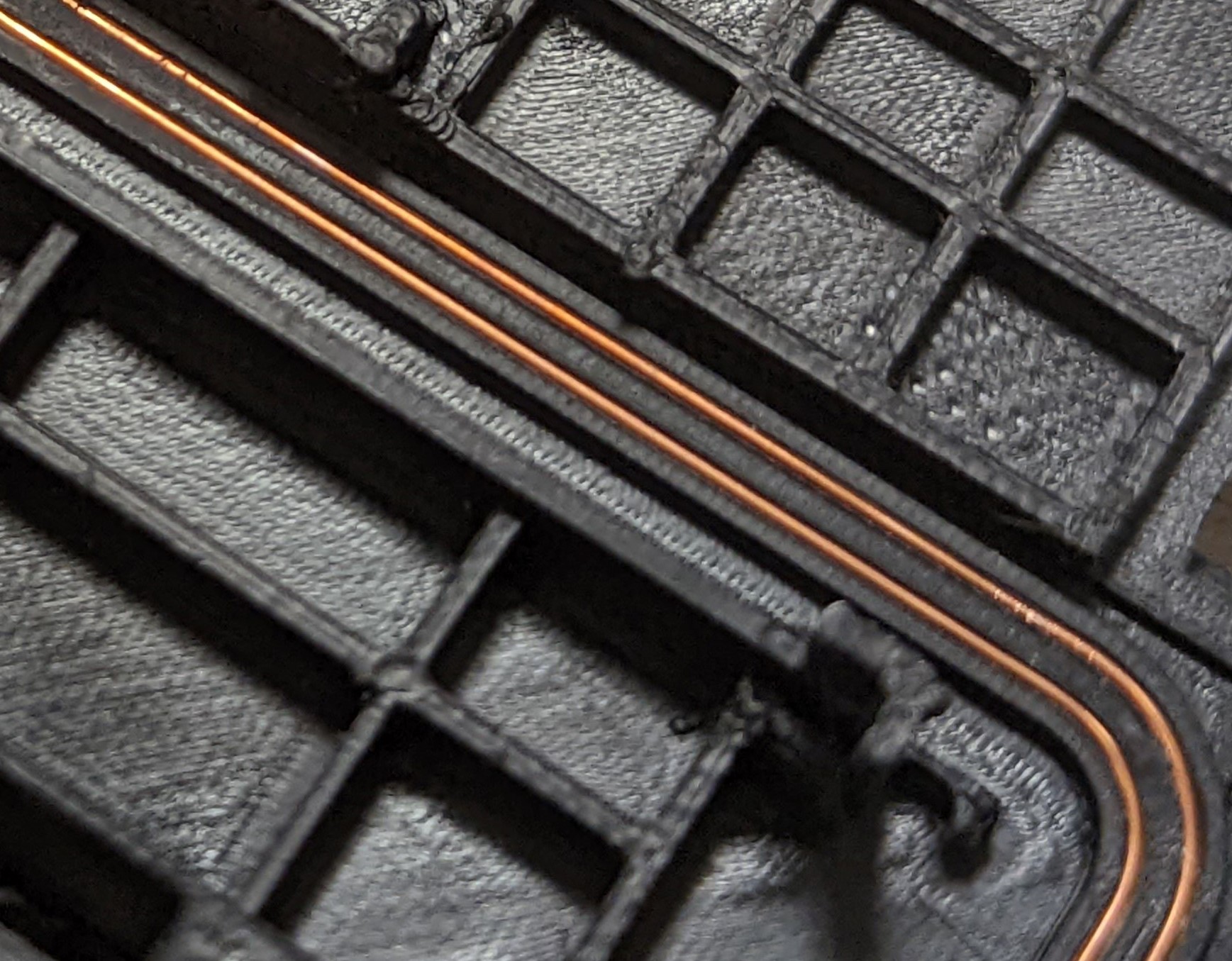
Ready to see this in action?
Contact us to discuss your project.