Why does wiring automation matter?
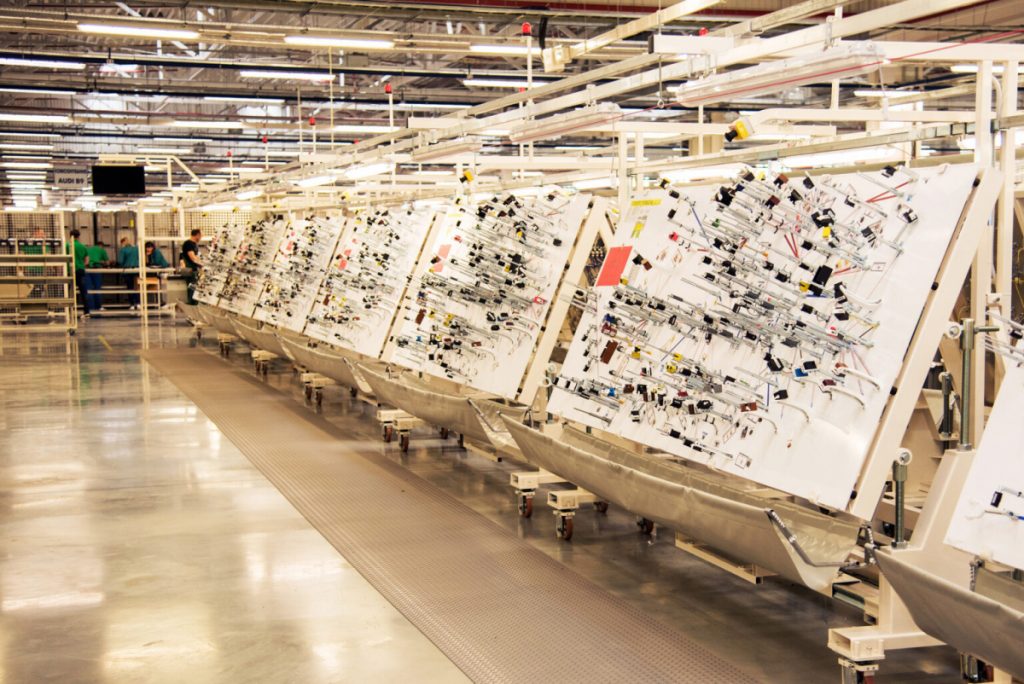
Wiring harnesses are critical components in many of the products we rely on, from cars and planes to white goods and consumer electronics, enabling electrical functions such as lighting, electric motors, and sensors. As such, wire harnesses play a key role in electrification, the Internet of Things (IoT), and Industry 4.0. In this blog, we will look at why automating the production of wiring harnesses – presently a labour-intensive process – is so critical and how it can act as a catalyst for more resilient supply chains, higher product quality, and further innovation.
Inside every vehicle, machine, or electronic product are multiple wires carrying power and data critical for operations. For instance, an average car can have over 3,000 wires weighing up to 60kg, while a typical passenger aircraft can have 500km of wiring, weighing more than 8 tons. These wires are typically collected into wire harnesses to consolidate them into confined spaces and maintain an orderly arrangement.
Wire harness production has traditionally been a manual operation as the harnesses are too flexible for robotic handling. As such, manufacturing has been outsourced to areas like eastern Europe and central America where there are skilled workforces but relatively low labour costs. A remote production strategy has met the needs of the industry in the past, but some recent challenges have exposed weaknesses in this traditional approach.
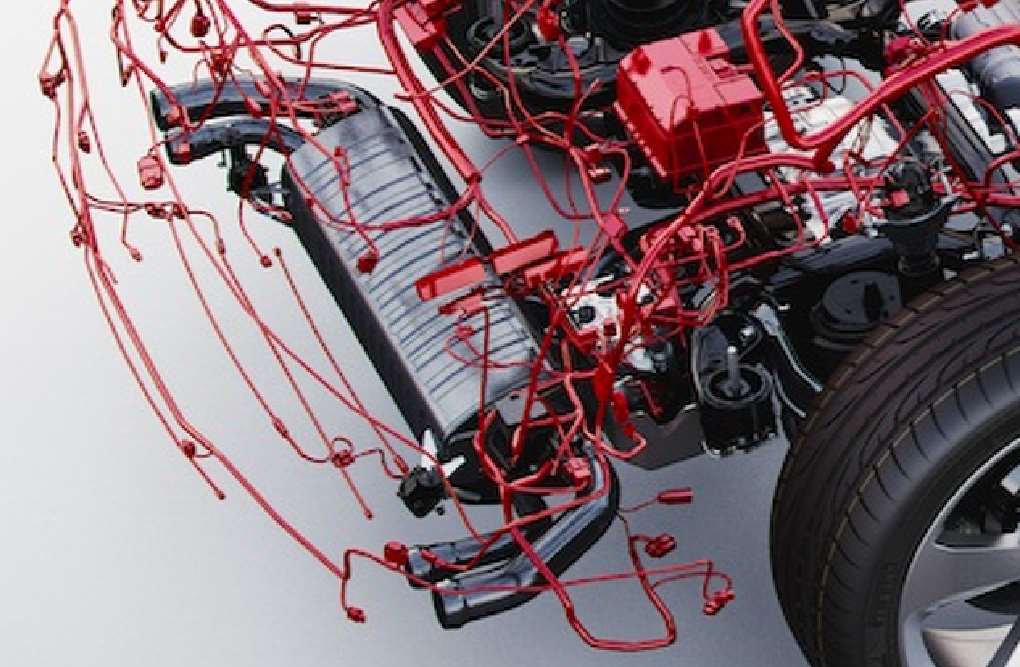
Issues addressed by automation of wiring
Supply chain challenges
The COVID-19 pandemic and the war in Ukraine have caused severe supply chain disruptions for original equipment manufacturers (OEMs). European car makers experienced shortages of critical components (including wire harnesses from Ukraine) that recently curtailed their ability to meet their production targets. According to Gartner, at least half of the top 10 automotive OEMs are considering bringing the design of critical components like chips in house by 2025. This “reshoring” strategy will help insulate them from supply chain volatility and component shortages in the future. It will also lower their environmental footprint by reducing the emissions associated with transporting components over large distances.
Product durability
All responsible manufacturers are concerned with the durability of their products. Manual assembly places stress on the wiring at the point of manufacture, and human error leads to poorly fitted, connected, and secured wiring. Along with environmental factors from vibration to rodents, there are many ways in which failures can be initiated. Such failures are difficult to trace, time consuming to repair and, in the worst cases, create significant safety issues. The U.S. Department of Transportation cites electrical systems as the second most likely cause of vehicle recalls.
Lightweighting
The manual handling of wire harnesses causes mechanical stress to wires from bending, twisting, and stretching. As a result, engineers tend to over-specify the wiring design leading to oversized cabling, extra weight, and higher costs. However, there is limited space for wiring in products and vehicles, and weight typically reduces performance and battery life making it vital to optimise wiring designs. Excess materials used for wire harness production also add to our carbon footprint and work against emission goals.
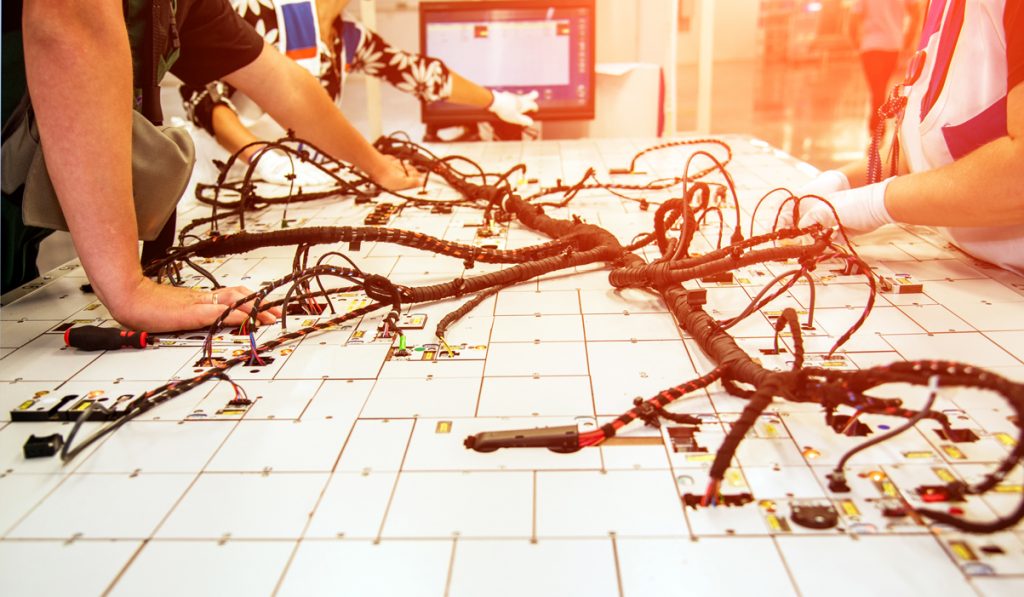
Automation methods
Several manufacturing methods have emerged in recent years intending to automate wire harness production with varying degrees of success but with some challenges. Solving these challenges could lead to great benefits for the industry, including vertically integrating wire harness manufacture with product assembly.
Some automation solutions are:
- Laser direct structuring (LDS) creates conductive tracks with excellent conductivity. However, the process is expensive and energy-intensive making it suitable for microelectronics rather than larger products.
- Printed electronics that are lighter and more flexible but are mainly limited to small consumer electronics.
- Large-area flexible conductors use additive or subtractive methods to lay a thin copper foil on a flexible polymer substrate. This method is suitable for high power and large structures but is difficult to change when designs are altered.
- Automatic block loader machines can help automate part of the manual production process, like cutting, stripping, and crimping. However, this technology doesn’t solve the fundamental problem of wiring harnesses having to be installed manually.
Q5D’s new approach
Q5D has developed a system for adding wiring directly to existing parts using additive manufacturing, laser sintering, and 5-axis robotics. Engineers scan the parts to create a digital twin and then design the wiring template using this model. The machine lays the wiring exactly where it’s needed, including wire traps that secure wires in position and safely separate them from each other. 5-axis robotics adds terminations precisely and automatically.
The wire harness manufacturing process has historically relied on manual methods with production centres located far from OEM sites. As a result, OEMs have faced supply chain disruptions that threaten their ability to meet their market demands. Some progress has been made to automate manufacturing using LDS, printed electronics, and other additive methods. However, a new approach from Q5D is revolutionising the wire harness manufacturing industry. The Q5D technology adds wiring to existing product components with maximum flexibility, thus keeping the wire weight and footprint to a minimum. Using this new method of wire harness manufacture, OEMs can “reshore” this element of their production and eliminate supply chain disruptions.
