How a wiring robot came to solve the electrical function integration challenge
How a wiring robot came to solve the electrical function integration challenge
Ready to see Q5D in action?
Contact us to discuss your project.
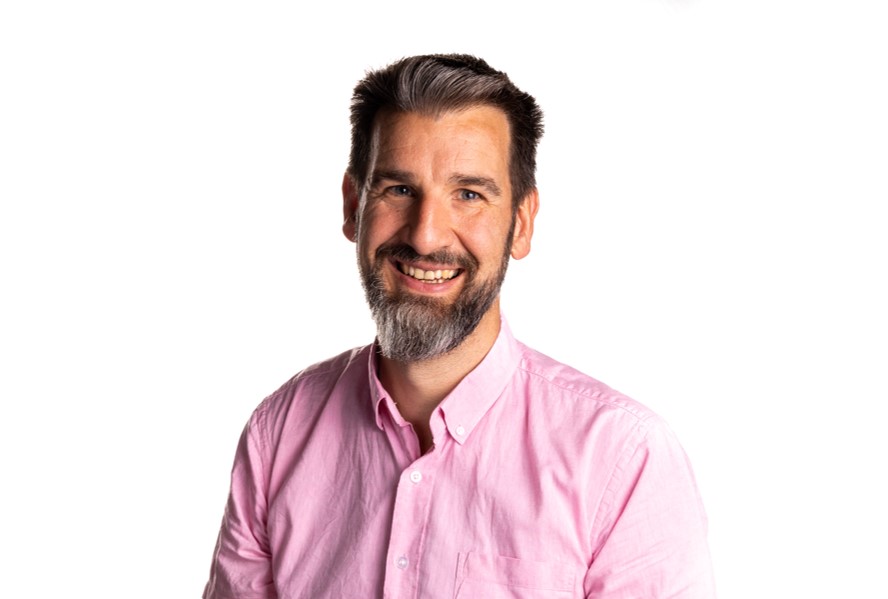
An interview with Chris Elsworthy, Q5D’s CTO.
Q5D launched its first 5-axis CNC additive manufacturing robot cell, the CY1000 in 2023. Designed to automate the difficult task of adding electrical connections to increasingly complex products, the self-contained CY1000 robot eliminates the need for expensive, bulky, and heavy wiring harnesses. Freelance technical writer and journalist, Robert Huntley caught up with Chris Elsworthy, Chief Technology Officer at Q5D’s Bristol, UK headquarters to talk about the company’s vision and some of the challenges it overcame to bring the robot to market.
ROBERT: When you designed the CY1000 robotic cell for automating wire harness assembly, why did you focus on this aspect of manufacturing?
CHRIS: During the development of other additive manufacturing machines, the focus was always on what the technology could produce. Often, the artifact you’ve made has no relevance to the real world. It’s more a demonstrable item of what our technology could do. I was looking for a way of additive manufacturing to help in manufacturing. What can additive manufacturing do that more traditional manufacturing techniques can’t do? There are things it can’t compete at, like injection molding, where the surface quality is outstanding, the repeatability is excellent, and the tooling used these days is extremely high quality. The volume and the price you can get a part out of an injected molding machine are unbeatable.
However, one of the most expensive things for injection molding is tooling. Whereas with additive manufacturing, you can make any shaped part without tooling. But it can’t compete on why someone might want that in an actual manufacturing situation, whether it be strength, surface finish, or volume of components.
The two things that additive manufacturing can do better than anything else is to be adaptable and produce anything you want by changing the program, not the hardware. So, if you come to that conclusion, who are you competing against? You’re competing against humans because that’s what humans do well. When you can’t automate something, what do you do? You put a human in place because they make decisions and process stuff quickly.
All the 3D printed parts I’ve ever made are because I want to screw a servo to it, put a motor on it, hold my soldering iron, or connect with something else in the bigger world. It’s that structural bridge between these electrical components, this mechanical interface. Additive manufacturing and wiring together means you’ve got a genuinely functional part, which isn’t just landfill, it’s an integral component of the machine, and that identified what I wanted to work on.
This 5-axis robotic cell enables bare or insulated wires to be used in an additive manufacturing process that
eliminates heavy, expensive, and potentially unreliable wire harnesses.
ROBERT: How difficult was it to go from the initial idea to a working prototype?
CHRIS: Additive manufacturing is generally a repetitive two-dimensional process where you use two-dimensional layers repetitively to build a three-dimensional structure. The electrical systems I’ve seen do that, just like PCBs do the same way, so you put a layer of PCB, a few wires in it, and it goes to the next layer. I wanted to get away from that approach, and one of the great things about additive manufacturing is you don’t have to be 2D. The challenge is not repeating two-dimensional layers because the best way to get a conductor from A to B in any three-dimensional space is usually a straight line or point-to-point. The light bulb moment was, let’s put two more axes in the machine, give it a full five degrees of freedom, and then suddenly we can build structures and put down electrical conductors in a much more precise manner. We can follow the contours of a part to put the conductor from A to B in a single filament rather than doing those stair steps. The challenge for us was to build that kind of electrical system and bolt it to a five-axis machine so that we could have ultimate control over the process. And that’s what we did in our prototype.
These robot heads, or end effectors, add copper conductors to products during additive manufacturing.
The conductors can be up to 3mm in diameter and bare or insulated wires can be used.
ROBERT: How did you approach the hardware and software design?
CHRIS: First, we looked at off-the-shelf single-board computers designed for industrial applications. Many were very mature, but we wanted to connect things that were outside their ecosystem. Then we looked at what we must do to allow that to happen. We found that we would only use 10% of the functionality these computers and that 10% wasn’t a perfect fit for what we wanted.
This led us to design our board in its entirety. We’re using an FPGA for the fast processing and originally put a microcontroller next to it, but it turned out to be difficult from an architecture perspective. In the end, we broke the electronics into two parts. We have a high-speed FPGA board, which is entirely our design and construction, and then we added a Raspberry Pi to do all the upfront processing. The Raspberry Pi does some maths, chunks the work together, and then inserts that into the FPGA. The FPGA then does all the real-time maths.
Our software is in three parts. We have the embedded software that the FPGA runs, which is all the real-time maths and stuff. The Pi is running the machine’s firmware, taking all the G-Code instructions, and passing them to the FPGA. And then, on top of that, we had the GUI, which is the interface between the human and what instructions get sent to the Raspberry Pi. We chose Raspberry Pi because of the value of it. Our original boards had microcontrollers, USB and HDMI connectors, and everything you could ever need to plug into a wider world, but it cost us thousands of pounds to develop that. Whereas the Raspberry Pi is £90, you get all that built-in, it’s all tested, and there’s a wealth of information on the net about how to use it, so it was a much easier way for us to optimize and develop.
ROBERT: Do you assemble all the electronics in-house or use a subcontractor?
CHRIS: The volume is low at present, so every component on our PCBs has been hand-assembled in-house. This is about the limit of what we should do manually, so when we increase the volumes, we’ll set up an SMT machine. Again, because of our low volumes, most of our components come from distributors. Obviously, with the recent supply chain issues, that’s quite a big topic. When we sourced all the components it was hard to get like-for-like. I think the problem is now easing a bit. Where we can, we’ve dual-sourced as much as we can. Not so much the integrated systems that we’re making and manufacturing ourselves; there are only a few replacement components unless you change the design. But with the more discrete things we’ve got in the machine, like the servo drives, contactors, and all that sort of stuff, they’re all dual-sourced.
ROBERT: What use cases do you foresee for electrical function integration?
CHRIS: Everything has wiring looms, so we have to be a little more focused rather than just saying we’ve built a machine for everything. We’ve picked aerospace, automotive, and military systems because those organizations have reasonable R&D budgets. I imagine that once the technology is used more widely, it will be the consumer goods, white goods with the real volume of wiring looms, which suffer from all the problems we’re trying to fix.
Control grips like this one can be made lighter, smaller, and more reliable when wiring is embedded within the product.
My history is in making handheld cordless products, so drills and things like that. One of the biggest failures is the wiring loom inside. Mainly because it’s a compact product, there are a lot of wires inside, and as they bring the two clamshells together, they often trap the wires between the two halves.
Clamshell designs, like this power tool, can be made far more reliable through precise positioning of conductors using additive manufacturing.
Our system negates that entirely because all the wires are positioned by robots. You can run all the stress and test analysis digitally before you finish the design, and the robot should do the same thing every time. So, once you have your design nailed down, you shouldn’t suffer from electrical errors in your products.