Four reasons why automating wiring harness production is critical to electrification
Four reasons why automating wiring harness production is critical to electrification
Ready to see Q5D in action?
Contact us to discuss your project.
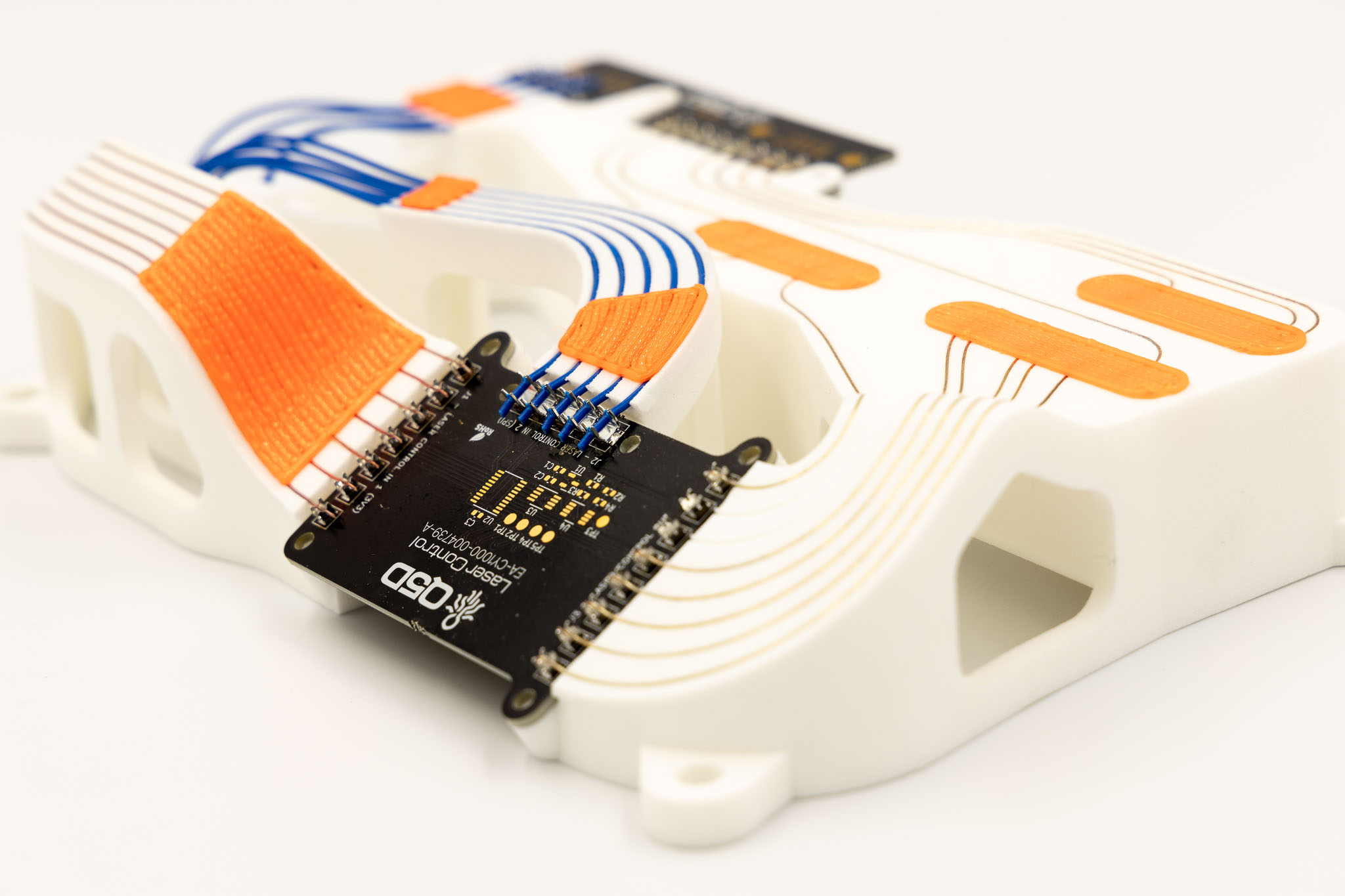
Electrification is a critical trend in the quest for a net zero economy. This process is accelerating, encompassing everything from transport to buildings, and industry. Wiring harnesses – the component enabling the transmission of power and data – are critical to this transition. Here Chris Elsworthy, Chief Technology Officer at Q5D, explains why automating the production of wire harnesses is essential to meet the growing industry demand.
1. There’s no electrification without wiring
Buzzwords like “electrification”, “e-mobility” and “electric vehicles” (EVs) are often used interchangeably. However, electrification – replacing fossil fuels with electricity as an energy source – extends well beyond transport. For example, the decarbonisation of buildings, which often goes hand in hand with the development of “smart buildings”, is another major driver behind electrification.
Electrifying our society is essential to reaching net zero by 2050. According to the International Energy Agency (IEA), the share of electricity in energy demand must increase by 3.5% per year over the next quarter of a century.
Wires – typically arranged in architectures called wiring harnesses – are the unsung heroes of electrification, enabling the transmission of power and signals. Perhaps unsurprisingly, demand for wiring is growing like never before. The expansion of the EV market contributes to this spike in demand, with a typical EV using almost double the number of wires than a traditional internal combustion engine (ICE) vehicle. According to a ResearchAndMarkets report, the global EV wiring harnesses and connectors market may reach $22.87 billion by 2031, growing by nearly 25% per year.
2. Wiring is becoming more complex
Look inside any EV, and you’ll immediately understand why electrification is causing wiring to grow in volume and complexity. According to Boston Consulting Group, we have entered the era of “exponential complexity in automotive engineering”. Consequently, demand for wiring continues to grow.
Added complexity derives from the EV drivetrain having to connect high-voltage batteries, inverters, and motors through a separate wiring system, in addition to the standard wiring harness found in ICE vehicles. The wire harness itself requires additional components and complexities to connect to the EV drivetrain. Additionally, lithium-ion (Li-ion) batteries – widely used in EVs – require a sophisticated battery management system due to their flammability, leading to added wiring complexity.
But the expanding demand for wiring extends beyond the electric powertrain. Vehicles are becoming “smartphones on wheels” with multiple electronic control units (ECUs) supporting numerous features, from parking assistance and memory seats to power steering and autonomous driving capabilities. All these features rely on wiring to function. Consequently, the ability to produce complex wire harnesses in large quantities is paramount.
3. Current wiring production methods have limitations
Using traditional ICE wiring harnesses for EVs would lead to higher weight and costs. For example, e-mobility experts Aptiv estimated that applying a typical ICE SUV architecture to an EV equivalent would result in a wiring system over 26 kg heavier, requiring 300 metres of additional wiring to guarantee the same functionality. Rethinking wire harness design to minimise weight and footprint is, therefore, critical.
Current wire harness production methods, which are predominantly manual, may struggle to meet the growing demand for wiring, both in terms of volume and complexity. Unlike the production of hydraulic and mechanical components, which, to a large extent, is already automated, wiring manufacture remains labour-intensive and depends on the availability of highly-skilled workers. Hiring and retaining skilled workers is becoming more challenging due to labor shortages and skill gaps, exacerbated by the COVID-19 pandemic.
4. Automation is key to taking electrification to the next level
Automating wire harness production can act as a catalyst for further electrification, in transport and beyond. A new approach to automation involves adding electrical functionality directly to components, significantly reducing the weight and footprint of wiring. This is now possible by combining additive manufacturing, laser sintering, and 5-axis robotics into one solution. Any part requiring wiring can be easily scanned to create a digital twin, enabling engineers to design the wiring around this model. This way, wire is applied only where needed, reducing weight and footprint, with minimal material usage and waste.
Another important implication of this new approach is that it virtually eliminates oversizing issues. Wiring is often overspecified to allow for manual handling and mechanical stress during production, transport, installation, and service life, leading to oversized cabling, added weight, and higher material and labor costs.
Another significant benefit of automation is the complete digitalization of the design process. Adding electrical functionality to virtually any type of material and surface (including curved) becomes much simpler, enabling original equipment manufacturers (OEMs) to take the “smartphone on wheels” concept further. A similar approach is applicable beyond transport to virtually any devices requiring electrical functions.
Conclusion
Electrification is here to stay and, as predicted by the IEA, will continue to expand and accelerate. Wiring is an essential component of any type of electrification and is experiencing unprecedented demand. Traditional wiring production methods were not designed for the degree of complexity and volumes required by electrified systems. Thanks to the latest additive manufacturing, laser sintering, and robotic technologies, automating wire production is now within reach and is ideally placed to support electrification. Automation can help make the process more accurate and repeatable, leading to better, safer products, fewer recalls, and more profitability.