Q5D to debut the world’s first wiring harness automation robot to take 200 USD off the cost of a car
Q5D to debut the world’s first wiring harness automation robot to take 200 USD off the cost of a car
Ready to see Q5D in action?
Contact us to discuss your project.
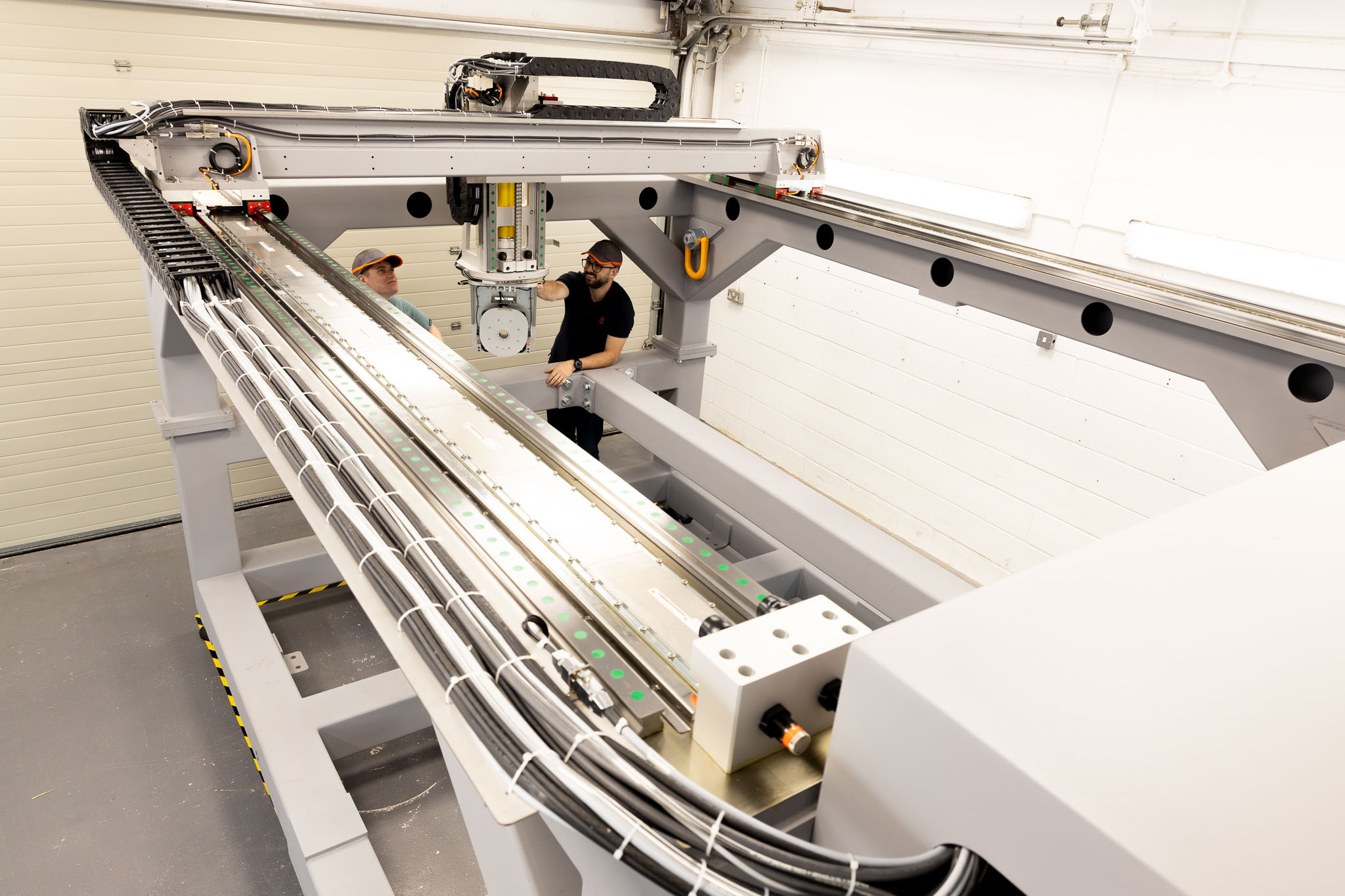
Bristol, UK, 28, March, 2025: Q5D Technology, pioneers of hardware and software tools for robotic wiring harness manufacture, has taken delivery of the core structure of frame and drives for its latest and largest to date wire harness automation robot at its Bristol headquarters in the UK. The frame of the robotic cell will undergo final assembly and be ready for service as the world’s most comprehensive wire harness automation robot, dubbed the SQ25W, in the late spring this year. The machine enables automotive manufacturers and Tier 1 contractors to save wiring space, cut costs, eliminate wiring errors in assemblies, and onshore manufacturing to minimise supply chain risks. The robot also reduces the factory space needed for vehicle manufacture. Cost savings for harnesses are conservatively estimated at 200 USD per vehicle. High volume car manufacturers could achieve annual savings in billions of USD by adopting the technology.
The SQ25W is designed for automating manufacture of larger wire harnesses and with a build volume of 2.5m x 1.5m x 0.15m. This new model is large enough to accommodate a complete vehicle headliner and assemble the wiring directly on to it. Headliners face severe space constraints in accommodating wiring for internal lighting, infotainment, noise suppression technologies, microphones, and multiple sensors, including a growing number of cameras and safety devices. The robot cell adds insulated wires directly to product assemblies, securing them in place and terminating the wires to connectors. The completed assembly is electrically a drop-in replacement for existing designs. The integration of wiring onto the component saves wire assembly labour, and eliminates the need for clips, tie wraps, and NVH (noise and vibration) related components.
The SQ25W features a positioning speed of up to 4 metres/second and can deposit wires at 1 metre/second, making it more than twice as fast as the earlier development models. In addition to head linings, the robot can be used to add wiring to large 3D non-planar products, such as drone wings. Its X-axis can be expanded to any length by placing a conveyor belt or robotic platform underneath and the machines can be integrated into existing production lines. The SQ25W is controlled via CAM instructions derived from a digital twin CAD model of the wire loom. A touch screen, which can be remotely monitored and controlled, provides an overview of the manufacturing platform status and performance, programme validation and simulation features.
Simon Baggott, CMO of Q5D, said: “We’ve been closely engaged with four of the world’s leading vehicle manufacturers and a similar number of their Tier 1 automotive suppliers over the last few years. The SQ25W has been designed in response to their needs. Automation, onshoring and cost reduction are high on the agenda of these companies and this new robot delivers all three, and more.”
Customers can evaluate the SQ25W’s performance in their specific applications at Q5D’s technical assessment centre in Bristol, UK.