Mass customisation
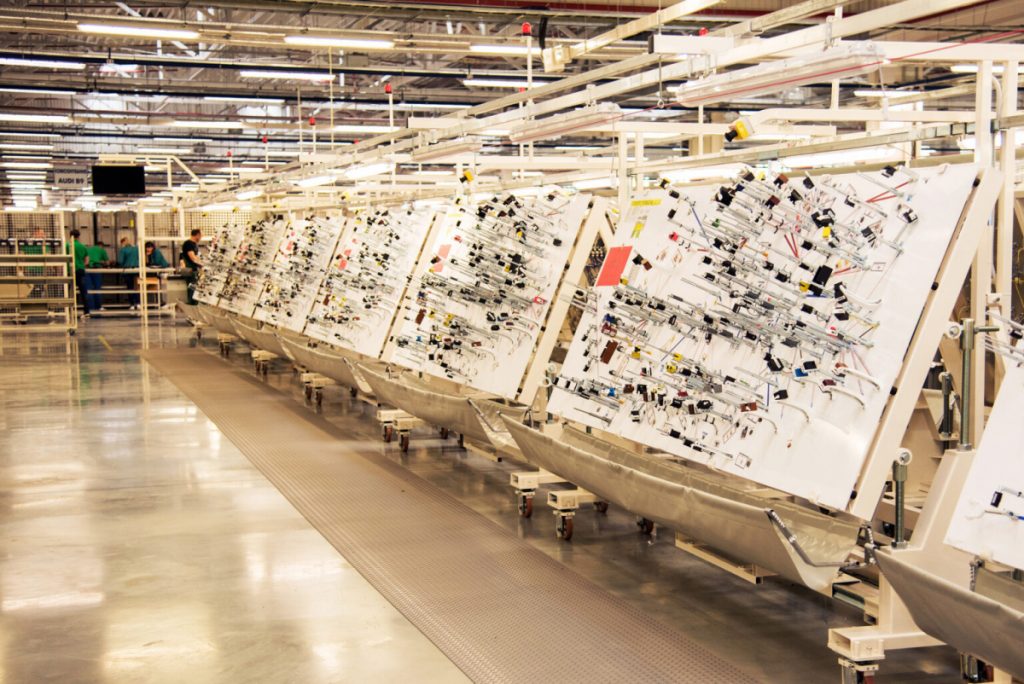
Mass customization is that ideal world where the customer can enjoy a personalized product, whilst the manufacturer retains the advantages and low unit costs of mass produced items.
Just-in-time (JIT) manufacturing has often been adopted as a means of achieving mass customization, with varying degrees of success for both the customer and the manufacturer. One of the consequences of JIT manufacturing is the reliance on the supply chain.
Products that need electrics in order to function – and that’s most products these days – have proven to be especially resistant to mass customization. Wiring is complex, and usually hand made. As a result the supply chains are typically long as are the lead times. This results in a need to keep variations small in order to avoid inventory and obsolescence costs. The more variations there are the more likely it is that some will end up sitting on expensive warehouse shelves until it is obvious no one wants the part.
More and more functions on more and more products require wiring. Electrification, the Internet of Things and Industry 4.0 are just three trends that fuel the ever increasing the demand for sensors, motors and other electrical functions to be included in products from dishwashers to aircraft. Electric vehicles need more temperature sensors (to condition the batteries) than internal combustion vehicles. Keeping up with this demand is fueling the explosive growth in the demand for wiring harnesses.
It is clear that the demand for wiring harnesses and the demand for mass customization are incompatible with current manual methods of manufacture. Hand assembling wiring looms and then hand assembling those looms into the final product is not productive enough.
Q5D’s approach
Our automated manufacturing cells can add wiring, conductive tracks and terminations to complex shaped parts made from metal, ceramic or polymer materials. The 3D polymer additive fused filament fabrication can be used to anchor the wire, insulate connectors and tracks or add features like fixing bosses to the basic part.
The CAD/CAM robotic additive manufacturing approach means that almost infinite variation is viable. The small (2.2m x 2.3m) footprint of a cell means that co-location with final assembly is realistic. Mass customization of electrical products is finally a realistic commercial proposition.