Why Tesla’s wiring patent points to something important for the whole industry.
Why Tesla’s wiring patent points to something important for the whole industry.
Ready to see Q5D in action?
Contact us to discuss your project.
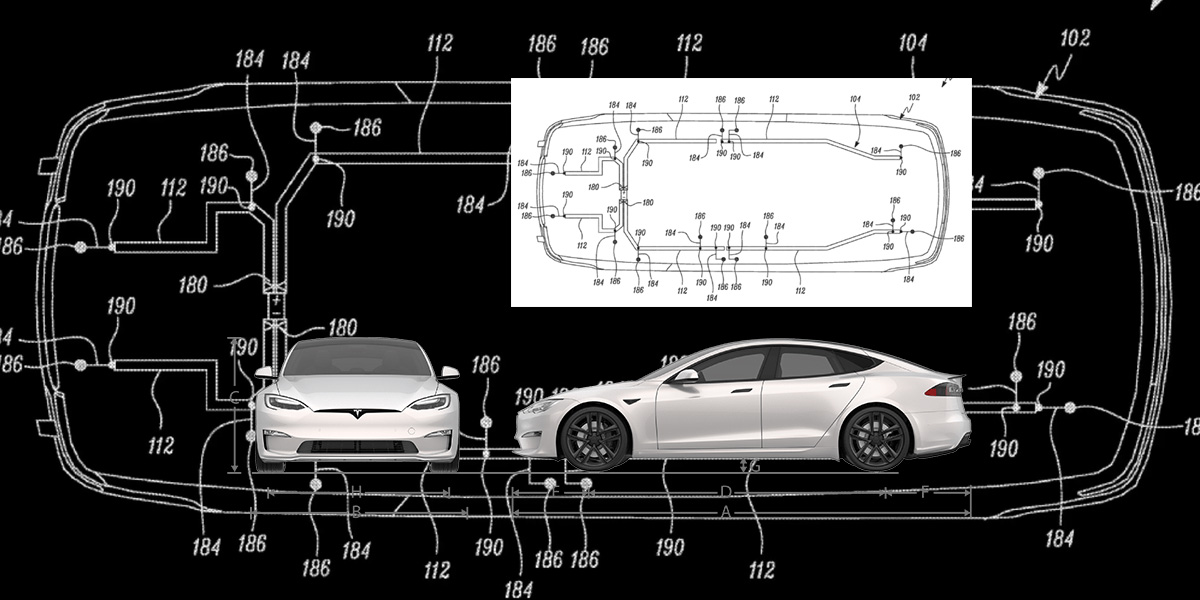
Tesla’s patent points at how they are thinking about some of the problems facing automakers generally. Tesla’s patent demonstrates their focus on simplifying the wiring harness, which helps with weight and cost reduction. However, on its own it may not be enough to address tone of the biggest questions facing the automotive industry today, which is “Who will build the wiring harnesses?” Finding the answer to this question was why Q5D was created. Our vision is to automate wire harness manufacturing throughout.
The last few years have seen significant events that have placed great stress on automakers. Both the pandemic and the war in Ukraine led to huge supply chain disruptions. These events highlighted a couple of problems that had been growing in importance for some time prior to 2020 and have continued since; the shortage of labour; and the growth in demand for wiring.
Even without the exceptional supply chain shocks of recent years, there isn’t enough labour to meet the demand of electrification of transport. A recent survey of over 40,000 employers in 41 countries by the talent acquisition agency Manpower found that 75% of employers were having difficulty finding staff. Engineering and Manufacturing both featured in the top five most difficult to fill disciplines.
Electric Vehicles (EVs), automated driving and advanced infotainment systems are driving a significant increase in demand for more wiring in cars. Zonal architecture reduces the amount of wire needed. Reports have suggested that the reduction on a vehicle like the Tesla model 3 is close to 50%, bringing the wiring down from 3km to 1500m.
Zonal architecture obviously saves material cost and weight which is especially important in EVs, but it also reduces labour content, perhaps the most important consideration given the sheer amount of labour needed. Heisler et al found that 90% of the process of assembly was done manually. (Heisler, P.; Utsch, D.; Kuhn, M.; Franke, J. Optimization of Wire Harness Assembly using Human-Robot-Collaboration. Procedia CIRP 2020, 97, 260–265). The factory that makes the wiring harness often employs more people than the assembly plant that builds the car.
Tesla’s patent demonstrates their focus on simplifying the wiring harness. Assembling wiring harnesses is skilled precision work, but very repetitive. The combination of the type of work and the shrinking labour force described by Manpower Group and widely accepted means the pressure to reduce labour content further will remain.
Automation of the majority of the assembly tasks that remain manual in making a wire harness is the answer. Q5D’s automation approach and the various techniques we are developing EVs we estimate will reduce by 80% or more the labour content compared to current manufacturing methods. This may also enable a wider supply chain simplification with wiring integrated into products rather than being a standalone process needing to be carried out in a remote, low cost location.
Simplification is an important element in enabling automation, and that’s what makes Tesla’s patent so interesting. Combining simplified wiring harnesses and automation of the majority of assembly tasks, as we can at Q5D, will enable the continued electrification of transport at an affordable cost.