The last automation frontier
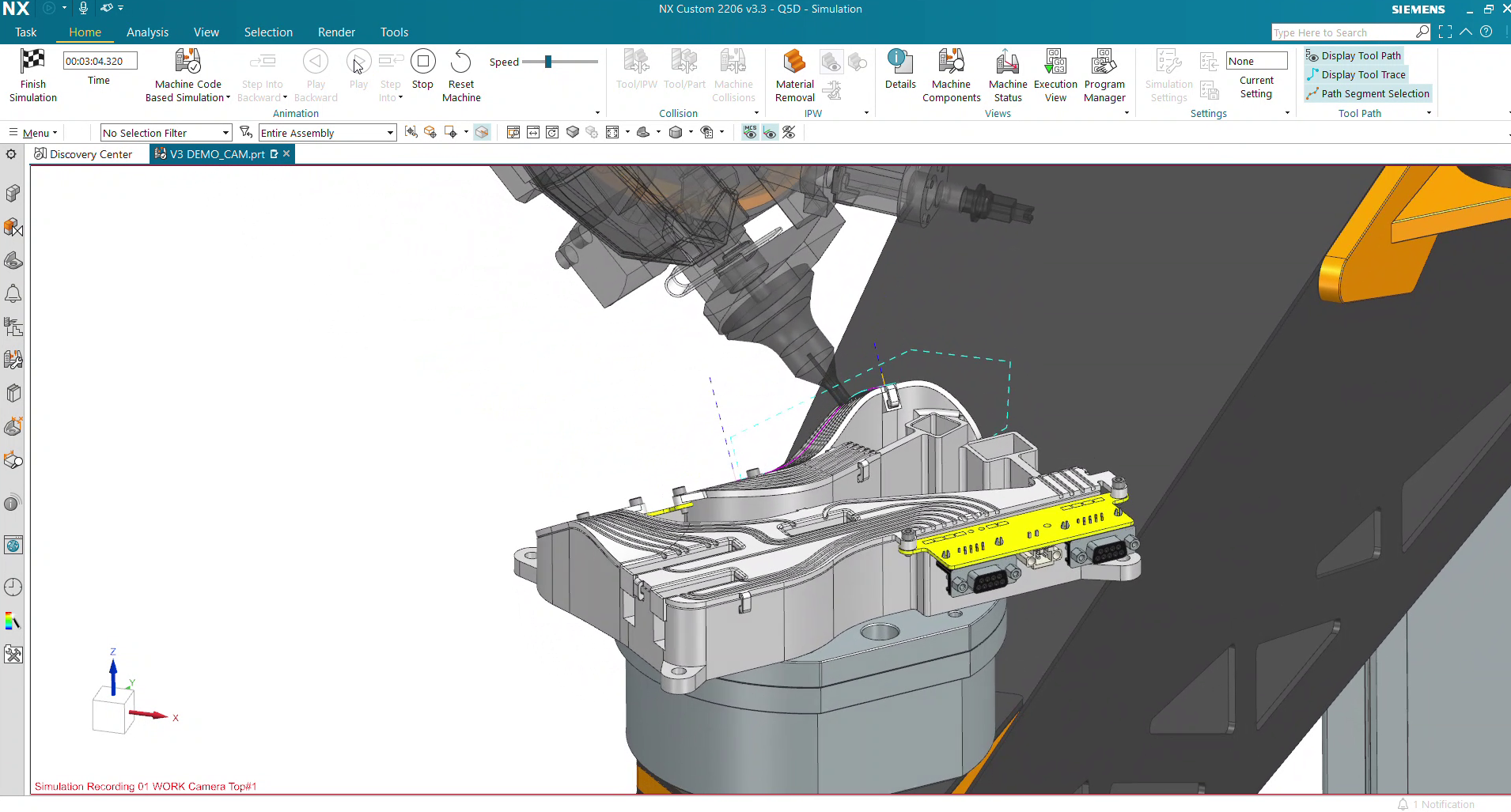
Wiring harnesses are found in just about every modern device. Some are incredibly complex. A modern car wiring might have more than 3000m of wire and hundreds of components. Amazingly though these harnesses are largely hand made. The productivity, cost and quality benefits of automation have bypassed this industry, and the hunt for affordable skilled labour in massive numbers have led manufacturers to locations ever more remote.
Factory in a box
Q5D’s robots make complete wiring harnesses or looms – not just parts of the harness – the entire harness, including terminations, splicing, protection and retention features. All controlled by CAD/CAM design.
Fully digital future
Hardware, Software and integration expertise combine in a project which intends to forever change the way wiring looms are made. Emixa and Q5D are in a collaborative project with the MTC to simplify the way a harness is created in CAD, fed to a machine through CAM and integrated into automated factories to produce a wiring harness without the need for low wage labour, simplifying and shortening supply chains in the process.
Space Saving
The unique gantry robot feeds wires in a pattern to match your design, conforming to an existing surface in your CAD model. These wires can be any common insulated or bare wires including twisted pairs. Wires on a substrate surface can be retained in features on the substrate or with adhesives extruded by the robot. The robot can also produce a product similar to a traditional harness but encased in a protective film. The resulting loom is lighter and uses less volume while being compatible with FEA simulation.
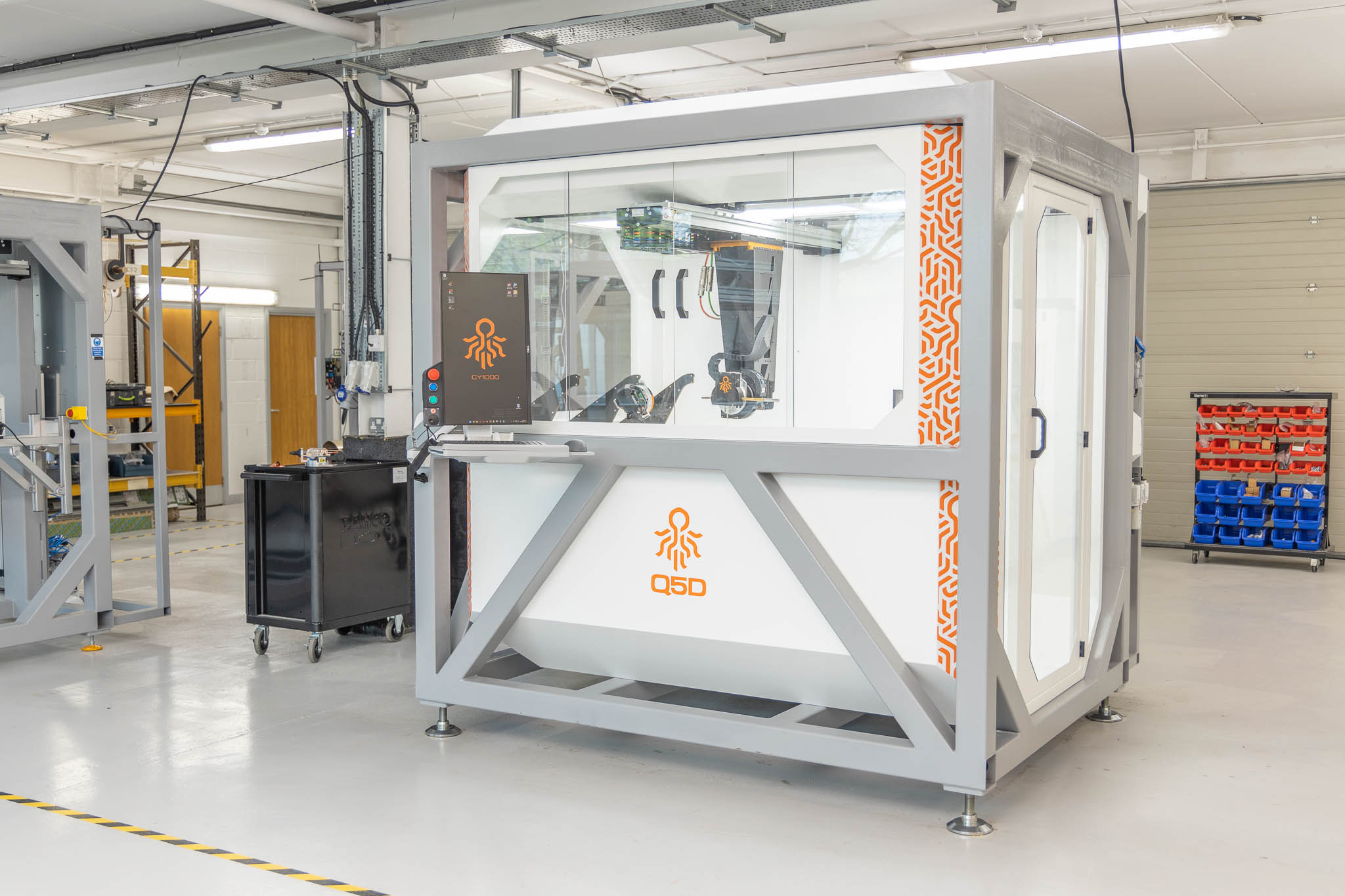
Can be tool free
The Q5D harness assembly method does not use a formboard or pinboard like most harnesses. The wires are connected to a substrate which already exists as part of the product. For example a door skin in a car contains controls, speakers, sensors and airbags. This door skin currently hides a loose harness but the Q5D method will attach the wiring to the hidden side of the door skin where it is protected and ideally positioned to carry power and data to the devices on the door skin. The conductors are protected and constrained by the door skin which, unlike a typical wiring loom, can be installed by a robot.
Full design control of shape, space and position
Currently a designer leaves space in their model for a harness which is specified through stages of requirements and schematics. Typically a 3rd party supplier manually creates a prototype and through some iteration it becomes a production which usually involves a very large facility and a large number of workers. 80% of the manual labour in car production is for the electrical harness.
The Q5D system is a 5-axis gantry robot running g-code programs generated in Siemens NX with an additive manufacturing module. A model made in NX CAD is loaded into NX CAM to build a series of tool paths, these are post processed and transferred to our machine. One worker can manage several machines which can integrate with fully automated factories.
Turn your wiring harness straight into a product
This automation will impact the supply chains of every industry. The Q5D platform will not require hundreds of staff in huge facilities, a machine attached to an assembly line can make any design variation just in time and at the assembly plant. Using our system, transportation of looms between supply and assembly lines is removed, storage of spare parts is no longer required and parts are optimised for end use, removing over specified wires and protective wrapping imposed by handling requirements. A single machine can supply a one off design every time just by sending a different program. This is the factory of the future.